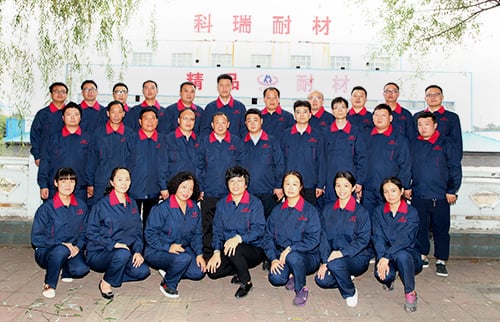
We are a refractory material manufacturer, with four major factories: heavy brick factory, light brick factory, monolithic refractory factory and fused-cast brick factory.
We promise to provide you with high-quality refractory materials.
Product introduction of graphite crucible
Graphite crucible is a crucible made of graphite, silicon carbide, clay, silica, wax stone, asphalt, tar, etc. The graphite casting crucible is made of graphite refractory with high purity, high strength and high density. Graphite crucible can be made into graphite crucible, graphite casting crucible and graphite oil tank through CNC processing.
Features of graphite crucible
- Good thermal stability of graphite casting crucible: special formula for the use conditions of graphite crucible for quenching and heating.
- Graphite crucible has good resistance to strong acid and alkali.
- Graphite casting crucible has good corrosion resistance and impact resistance, ensuring the reliability of product quality.
- The ash content of graphite crucible is less than 300pp to ensure that precious metals are not polluted during smelting.
- Good thermal conductivity of graphite crucible: it can greatly shorten the melting time and save energy.
Parameters of graphite crucible
Model | Upper port outside diameter ±2% | Thickness | Lower bottom outside diameter ±2% | Height ±2% |
1# | 67 | 8± 1.0 | 35 | 65 |
1.5# | 78 | 10± 1.0 | 60 | 80 |
2# | 88 | 10± 1.0 | 62 | 100 |
3# | 100 | 12± 1.0 | 75 | 115 |
4# | 115 | 12± 1.0 | 85 | 115 |
5# | 122 | 13± 1.0 | 85 | 138 |
6# | 125 | 14 ± 1.0 | 85 | 155 |
41# | 215 | 19~ 21.5 | 150 | 290 |
45# | 250 | 19~ 21.5 | 180 | 295 |
70# | 285 | 19~ 21.5 | 215 | 245 |
80# | 310 | 20~ 22.5 | 210 | 370 |
90# | 320 | 21~ 23.5 | 230 | 385 |
100# | 314 | 21~ 23.5 | 220 | 408 |
200# | 400 | 23~ 25.5 | 290 | 475 |
260# | 416 | 24~ 26.5 | 250 | 585 |
300# | 452 | 26~ 29 | 310 | 580 |
360# | 462 | 28~ 31 | 342 | 674 |
390# | 530 | 28~ 31 | 410 | 560 |
400# | 515 | 29~ 32 | 340 | 600 |
420# | 515 | 29~ 32 | 330 | 673 |
440# | 620 | 29~ 32 | 340 | 500 |
450# | 516 | 32~ 35 | 340 | 710 |
530# | 580 | 31~ 34 | 330 | 635 |
560# | 590 | 33~ 36 | 330 | 690 |
570# | 620 | 33~ 36 | 335 | 570 |
580# | 545 | 33~ 36 | 317 | 750 |
610# | 607 | 34~ 38 | 350 | 630 |
680# | 585 | 34~ 38 | 330 | 760 |
690# | 600 | 34~ 38 | 330 | 805 |
700# | 615 | 34~ 38 | 350 | 758 |
840# | 700 | 35~ 39 | 470 | 675 |
950# | 720 | 37~ 41 | 300 | 740 |
970# | 720 | 34~ 38 | 470 | 730 |
1100# | 715 | 35~ 39 | 478 | 846 |
1150# | 855 | 42~ 46 | 340 | 677 |
1200# | 780 | 36~ 40 | 450 | 752 |
1250# | 725 | 36~ 40 | 470 | 905 |
1500# | 784 | 37~ 41 | 450 | 890 |
1700# | 778 | 40~ 44 | 442 | 1050 |
2500# | 880 | 44~ 48 | 350 | 1150 |
Graphite Crucible Performance Index
Item | Ⅰ | Ⅱ | Test Method | ||
Forming method | Plasticity (S) | Isostatic pressure (D) | Plasticity (S) | Isostatic pressure(D) | |
Carbon content /% | ≥ 38 | ≥ 45 | ≥ 38 | ≥ 45 | GB/T 1655-2008 |
Bulk density /(g/cm3) | ≥ 1.70 | ≥ 1.85 | ≥ 1.70 | ≥ 1.85 | GB/T 2997-2000 |
Porosity /% | ≤ 29 | ≤ 21 | ≤ 29 | ≤ 21 | GB/T 2997-2000 |
Normal temperature compressive strength /MPa | ≥ 20 | ≥ 25 | ≥ 20 | ≥ 25 | GB/T 5072.2-2004 |
Fire resistance / ℃ | ≥ 1500 | ≥ 1500 | ≥ 1400 | ≥ 1400 | GB/T 7322-2007; Antioxidant glaze coating |
Precautions for graphite crucible
- Storage: Store in a dry place, not wet.
- Handling. Handle with care and avoid collision.
- Place. Use the correct crucible support and ensure that the crucible base is firmly in contact.
- 4. Loading. Carefully load the steel ingot or scrap metal into the crucible, and do not squeeze hard, nor insert and squeeze too tightly.
- Add melt. Use as little flux as possible.
- Cleaning. Keep the crucible clean, pour out the residual metal quickly after the operation, and carefully remove the residue.
- Drying and preheating. If the crucible is damp, it needs to be dried slowly at a temperature lower than 100 ℃.
- Removal of water. All water around the furnace shall be removed to avoid metal and water contact and explosion due to leakage.