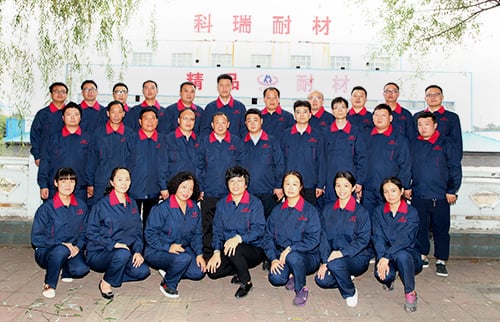
We are a refractory material manufacturer, with four major factories: heavy brick factory, light brick factory, monolithic refractory factory and fused-cast brick factory.
We promise to provide you with high-quality refractory materials.
Product description of Al-Mg refractory Castables
Al-Mg refractory Castables are prepared from electrofused magnesia, sintered magnesia, electrofused or sintered magnesia-aluminium spinel, electrofused corundum, alumina powder and high aluminium content powder. Depending on the quality of the raw materials used, it can be divided into: Castable common aluminium-magnesium alloy, Castable common high aluminium spinel, Castable alumina, Castable spinel, Castable corundum.
Application of Al-Mg refractory Castables
Ordinary aluminium-magnesium alloy casting is used for the complete lining of the continuous casting ladle.
Common high alumina Spinel is composed of high bauxite aggregates containing powder, bauxite and sintered Spinel containing powder. It is applicable to the full lining of the small and medium size continuous casting ladle, the permanent lining of the tundra and the lining of the electric furnace outlet tank, etc.
Alumina – Castables magnesium oxide aggregates consist of white fused corundum, flat alumina or high fused aluminium corundum. It is generally used for full lining below the ladle slag line on a large scale, with a service life more than 1 times that of ordinary Castable alumina-magnesia, and can also be used as a lining for other high temperature furnaces, vessels and ducts.
Castable Spinel Alumina and Castable Spinel Corundum are mainly used for lining large steel ladles, but also for lining the covers of high power electric furnaces.
Al-Mg refractory castables performance index
Item | AMC-70 | AMC-80 | AMC-85 | AMC-95 | |
ω(Al2O3+MgO)/% ≥ | 70 | 80 | 85 | 95 | |
Bulk density(110℃×24h after drying)/(g/cm³) ≥ | 2.6 | 2.8 | 2.85 | 2.95 | |
Normal temperature compressive strength, MPa | 110℃×24h after drying ≥ | 20 | |||
1000℃×3h after firing ≥ | 30 | ||||
Test temperature×3h after firing ≥ | 50(1500℃) | 50(1550℃) | 60(1550℃) | 60(1600℃) | |
Heating permanent line change, % | Test temperature×3h | -0.5~+1.5 (1500℃) | -0.5~+1.8 (1550℃) | -0.2~+1.8 (1550℃) | 0~+1.0 (1600℃) |